Functions of drilling fluids mud desilter
Drilling fluids mud desilter is the 3nd stage solids control equipment. It is usually used after desander. For mud cleaner used for oil and gas drilling field, 4 inch deciliter cone is the most frequency be used. It can remove solid particle around 30~70 microns.
Working principle of drilling fluids mud desilter
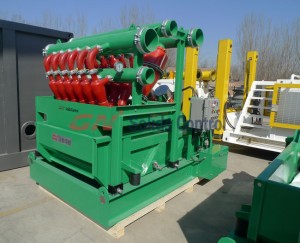
Main part of drilling fluids mud desilter is the hydrocyclone cone (desitler cone). It is a kind of pressure device. The separation process is carried out by employing centrifugal forces. Under pressure, drilling fluid with solid particles will flow into the mud desilter cones, after high rotation, bigger and heavier particle will be threw to cone wall, then slide down till drop in apex and separated out. Clean fluids will be moved out from cone top port. So, there will be 2 rotary gas flow in the drilling fluids mud desilter cone, one is liquid contains quantity big solid flow down as cyclone, the other is smaller solid mixed with gas go up as bow wave.
The angle of the fluid entry has been specifically designed to facilitate the flow and separation. The Cones are made of high durameter polyurethane with optional steel inserts, which ensure consistent productivity.
Desilter Cones remove fine sand and silt down to 30 microns.
Desilter Cones are available of 4″ size that have a 2″ inlet and a 2″ outlet.
Available models of drilling fluids mud cleaner
From design, there are mainly 2 types of mud desilter: with under flow shale shaker or without under flow shale shaker. For different capacity, the desilter cone can be used from 4 each to 24 each. Users can choose suitable models per his jobsite detailed condition.