GN focus on drilling waste management
Oil and gas producers face a significant problem with managing the waste generated in the drilling process. A single well can produce up to 1,200 tons of waste. This waste is comprised of drilling mud, which is injected into the well to lubricate and cool the drill head, and drill cuttings – the broken bits of rock and soil cut away in the drilling process and circulated up to the surface by the mud.
The oil content of this waste ranges from 10-30%, representing a significant cost if not recovered. Furthermore, disposal of drilling waste is receiving intensifying scrutiny from regulators and environmental agencies. Historically buried or landfilled, the high oil content in drilling waste has been proven detrimental to the environment
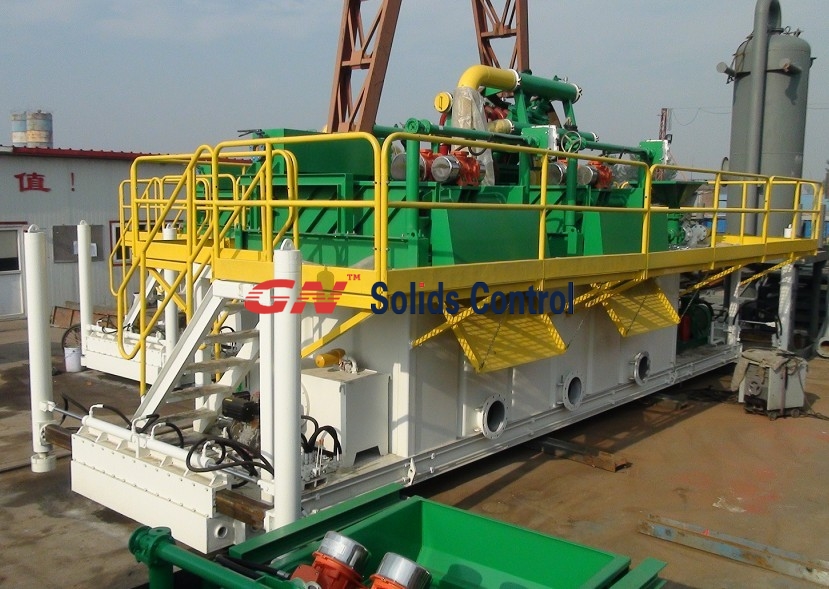
Before the introduction of mechanical solids-removal equipment, dilution was used to control solids content in the drilling fluid. The typical dilution procedure calls for dumping a portion of the active drilling-fluid volume to a waste pit and then diluting the solids concentration in the remaining fluid by adding the appropriate base fluid, such as water or synthetic oil.
Using solids-control equipment to minimize dilution has been a standard practice for the drilling industry for more than 60 years. Equipment and methods have changed over that time, but the fundamentals behind the process have not:
Solids concentration matters—increasing solids content is detrimental to fluid performance.
Economics matter—mechanical removal of solids costs less than dilution.
Volume matters—the volume of waste generated is indicative of performance.
Size matters—fine solids are the most detrimental and difficult to remove.
Stokes’ law matters—viscosity and density affect gravity separations.
Shaker-screen selection matters—shaker screens make the only separation based on size.
Footprint matters—the space available for equipment on rigs always is limited.
Increasing solids concentration in drilling fluid is a problem for the operator, the drilling contractor, and the fluids provider. It is well established that increasing solids content in a drilling fluid leads to a lower rate of penetration (ROP). Other problems that are related to excessive solids concentration include:
High viscosity and gel strengths.
High torque and drag.
Lost circulation caused by higher equivalent circulating density (ECD).
Less efficient drilling hydraulics.
Abrasion and wear on pump fluid ends.
Production loss caused by formation damage from filtrate or solids invasion.
Stuck pipe caused by filtrate loss.
Poor cement jobs caused by excessive filter cakes.
Generation of excessive drilling waste.
Higher drilling-fluid maintenance costs.
GN provide Solid control equipment and package solution for Drilling waste management